Prototyping is one of the biggest challenges when any bike company is trying to create their latest and greatest bike. More often than not, it has taken weeks or even months to simply transfer the original drawing on paper to a bike ready for testing.
Then that process can be repeated multiple times due to refinements and unpredicted ride characteristics. That is why it can take years for a bike to come to market but, that is all changing….
Before we move on to the more modern techniques let’s talk about the current process.
The most current company actively going through a classic prototyping process is Intense bikes. They have publicly been working on a prototype for over 2 years now. While it may never make it into production, they are still a great example.
By using their team riders Aaron Gwinn and Dakota Norton, Intense have set out to make their fastest bike ever. To do this Jeff Steber (founder of Intense) personally designs and welds alloy prototypes in his factory in California. Using a jig to ensure the bike matches the required angles pieces of alloy are accurately measured and moulded to create a bike.
Alloy is used for prototyping because it is a relatively cheap and malleable material. If you look at the price of a bike, more often than not the cost of prototyping is included. So if a manufacturer uses a more expensive material that takes more time then your new bike is going to cost a lot more.
The other reason a manufacturer like Intense will use alloy is because they can turn around new frames in a relatively quick fashion. Racers feedback can be taken on, implemented and new frames can get on the plane for the next race. It also means that if there is a failure at a race, a local welder may be able to fix it on the ground (this has happened before).
Now, let’s talk about the infamous black plastic A.K.A. Carbon Fibre.
To create a carbon fibre frame using traditional methods can cost upwards of twenty thousand dollars for a mould that may only last two or three frames. Unless you are like Hope and can create the mould in house, it is not a cheap exercise. Even brands like Forbidden are looking to use alloy for prototyping as the carbon mules are too costly.
Carbon fibre sheets and the resin is expensive and you need to hire speciality staff to work with the material, all costs that add up. The material is not the best when it comes to testing durability either as it tends to catastrophically fail on occasion.
In 2020 we saw the birth of Atherton bikes, a company that used modern technologies to revolutionise mountain bike manufacturing.
Using additive manufacturing (3D printing) to create titanium lugs at major tube junctions like the head tube, bottom bracket and drop outs. In between these lugs are carbon tubes to join the bike.
A huge benefit of the additive manufactured lugs is that with the press of a button new junctions can be printed overnight and a completely new geo can be created. The tubes of carbon can be individually easily tuned for certain flex characteristics, strength and ultimately reliability.
In 2022, we saw Finn Illes aboard a new Specialized that appeared to use the same system. It was a big deal because this was the first time that we had seen this prototyping method implemented by a larger mainstream company. By using this manufacturing style they are able to tweak the bikes geometry and kinematics rapidly and effectively.
Now in 2023, Pivot have followed suit with their new DWF6 prototype they are making leaps and bounds in no time at all. Pivot are able to make dropouts with adjustable chainstay positions, tweak idler positions and leverage ratios at the click of a button. While it still takes around 90 hours to make the frame, it is a hell of a lot quicker than older methods.
The big thing to take away from Pivot’s endeavours though, this bike will be a fully carbon frame when produced. While, personally, I think the lugs look cool a fully carbon frame is easier to manufacture in larger numbers. That expensive mould I was talking about before will only need to be created once and will be used for more bikes. However, thanks to the faster refinement, research and development will take less time and reduce the overall cost of a frame.
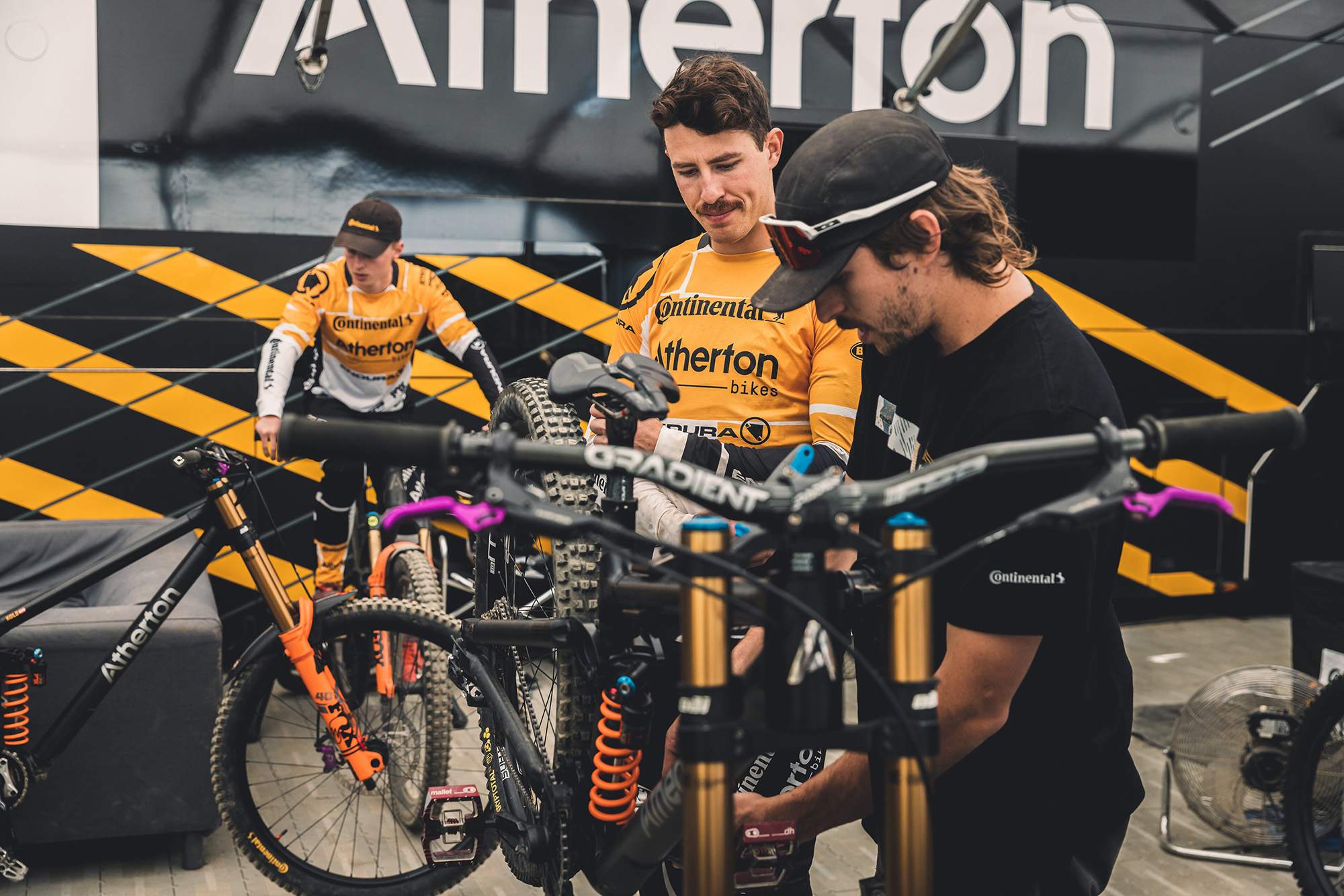
We know on good authority that many other brands are looking at these new methods for development to reduce costs, time and waste. There will be more of these lugged frames appearing at the races and riders will be pushing them hard. We expect to see some more wild designs and bike technology progressing faster thanks to these new techniques and we are damn excited. [R]